A tectonic shift in how products are made
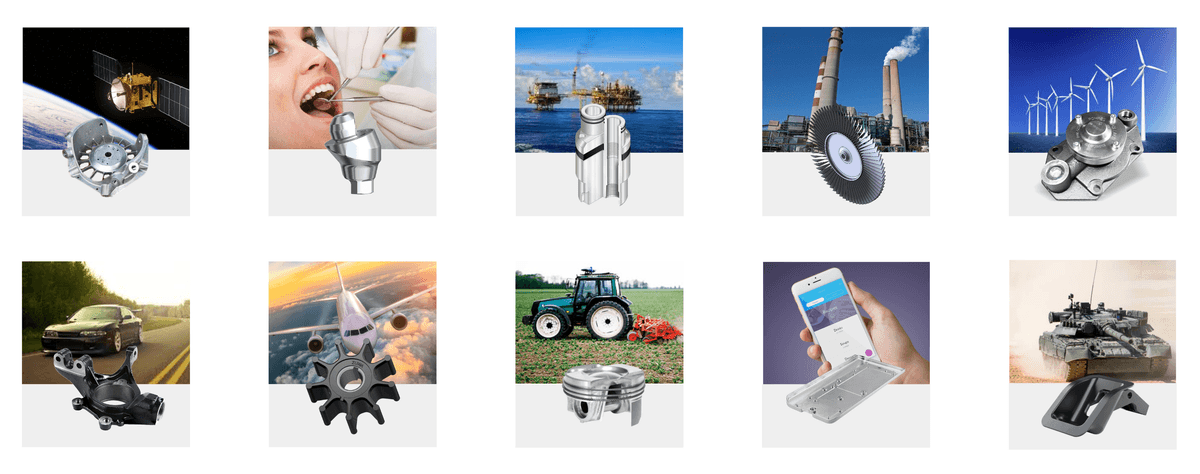
The world of precision manufacturing is currently undergoing the most profound changes seen since the rise of China in the early 1990s. Talent shortage, climate targets and growing product complexity make it harder than ever to go from design to production. Existing software is dated and unable to consider how design affects manufacturability and cost. To close the gap between design intent and manufactured outcome, and secure the reindustrialization of the Western world, we need a new technology paradigm to lead the way.
The largest market you've never heard of
Precision machining is likely one of the biggest market you’ve never heard of. With more than half a trillion U.S. dollars worth of machined components being made every year, this market has a profound impact on modern society and our quality of life. It sits at the very heart of the real economy, and employs tens of millions of people globally. Precision components are essential to the making of everything from hip joints and dental implants - to wind turbines, satellites and electric vehicles. Even smartphones.
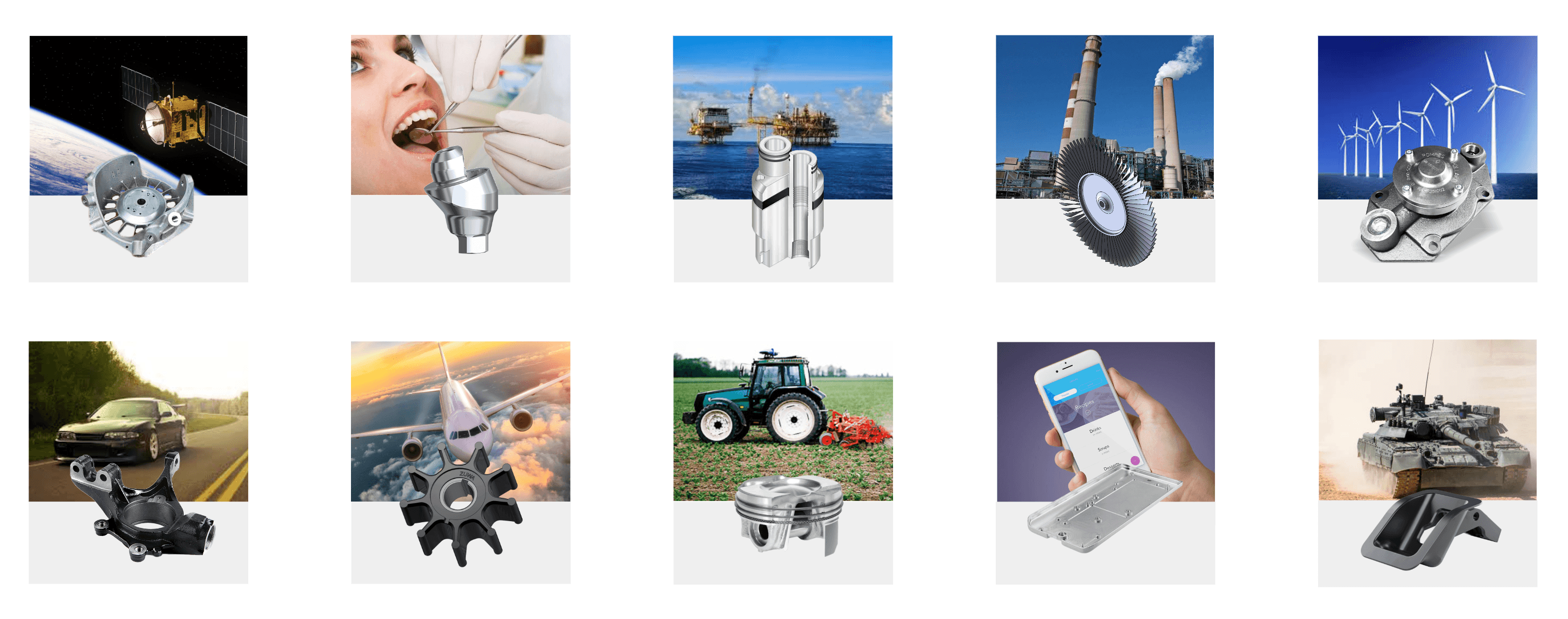
Right now, we are in the middle of a tectonic shift in how, by who, and where these kinds of products will be made for the next 50 years, driven by four mega trends.
- Manufacturers face an accelerating talent gap that threatens business continuity. More than 25% of the key employees are older than 55, and many are already at retirement age. 70% of teenagers do not want a career in manufacturing, and more than one third of open job positions are never filled.
- The pursuit of net zero carbon footprint is simultaneously redrawing the global supply-chain map, as well as becoming a license to operate. 80% of Fortune 1000 manufacturers are now strategically investing in localizing their supplier base to gain better control of their supplier base and reduce transport footprint. More than half of manufacturers are already actively culling suppliers who can’t keep up with emissions reduction targets.
- Advances in new production technologies, such as composite materials and 5-axis CNC machining – which are critical to the shift to sustainable production – remain out of reach for many manufacturers. Not to mention hardware startups. Existing software does little to lower the barriers to access to the benefits these technologies offer. The result is that more than half of machined components are prepared for production manually on the shop floor.
- COVID-19 fundamentally raised the bar for how and where people want to work. Manufacturing included. Employees now expect work to be much more collaborative, seamless and accessible. From anywhere, enabled by modern software that offers high degrees of automation for repetitive tasks, and little to no waiting times between action and outcome.
A broken feedback loop
Anyone who’s been bold enough to pursue a hardware idea will tell you how painful it is to go from design to finished product today. A majority of hardware innovations fail because the team underestimated how their design needs to translate into a real product. Manufacturing considerations aren’t properly considered until it’s either too late or expensive to change. The way we develop hardware is missing a fundamental puzzle piece: product industrialization.
In a nutshell, product industrialization is the process of transforming a product from prototype to being mass-produceable. Typically by streamlining design, materials, and manufacturing process to achieve efficient, cost-effective, and consistent production quality.
To illustrate why understanding manufacturability early isn’t just important, but mission critical, consider the following conceptual illustration of design options and cost of changes.
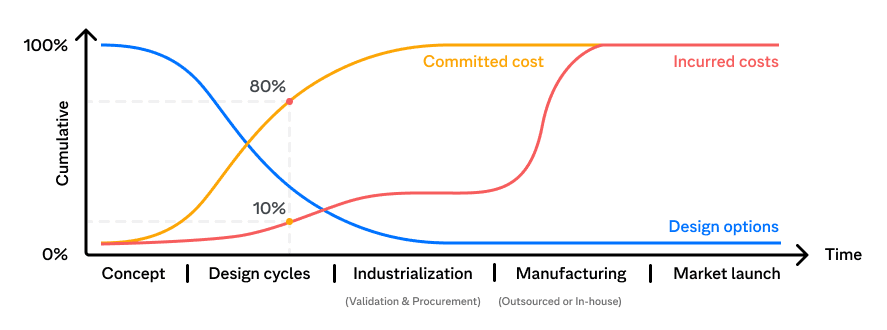
It is at the earliest stages of development that we have the most leeway in addressing design issues and ability to mitigate them effectively. But, even with this insight at hand, many manufacturers are faced with a reality that make it very difficult to act on it.
Too few employees are experienced in how part design affects manufacturability, and fewer still know how to program the machines that are used in production. As a result, designs are rarely made with manufacturability or marginal cost in mind. This leaves manufacturers with two hard choices. Accept multi-month delays in time to production that follow redesigns, or give in to significantly higher than expected marginal costs that can make or break the unit economics entirely.

Making matters worse, the existing software solutions are more than 40 years old, and provide little in the way of collaborative workflows, meaningful levels of automation or relevant manufacturability feedback. The failure of existing software to deliver this feedback loop poses a direct threat – not just to manufacturers, but the real economy at large.
If we allow the talent gap to continue to grow, we jeopardize the re-industrialization of Europe and pursuit of net zero emissions for one of the world’s largest global markets. Product industrialization must become an integral part of the hardware development process. To make this happen, we need an entirely new core technology paradigm. A paradigm that empowers and encourages more people to go build real, game-changing products where the deck isn’t stacked against them from the get go.
Product industrialization. Reimagined for teams
Today, the process of taking a product from design to manufacturing is a lot less streamlined than most people realize. Despite 3D models and 2D technical drawings being the focal point of the product in development, the vast majority of people who need to engage with them don’t have access to meaningful tools that enable them to interact with the data intuitively. The CAD software - and the associated desktop hardware - required to interact with 3D data is either much too expensive to procure unless the user will be designing parts day to day, or much too complex to use without extensive training.
Instead, manufacturers fall back on a combination of Teams meetings, PowerPoint presentations, Excel spreadsheets and email threads to try to strike a balance between design aesthetic, functional requirements and cost of production. PowerPoints are used to display screenshots of 3D models taken from the CAD software, while spreadsheets are used to store manufacturing requirements that are otherwise found on the technical drawing directly. Neither of which offer any possibility to easily explore how changes to a design or requirement affects manufactured outcome.
This workflow drives a lot of friction, because critical information isn’t readily available or actionable to everyone who is part of moving the product development process forward. For precision machined parts, this results in 20-30% higher marginal costs, on average, compared to what they could be.
Imagine instead if you could simply drop a 3D model into a web browser, and within seconds receive key insights about potential design issues, how your design drives marginal costs and how to adapt your design to find the right balance between performance requirements, design and cost. All of which are based on real, underlying manufacturing strategies that can also be used to run production. And, better yet, what if all of these insights were also accessible to everyone on the product team, at the same time, from any device?
This is what we’re building at Encube: the first truly collaborative, cloud-native, real-time Computer-Aided Industrialization, CAI, platform. A platform and workflow that integrates seamlessly into the product design cycle and helps connect the dots between CAD, CAM and CAE.
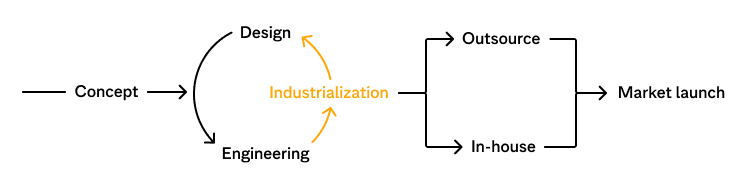
The innovation that sits at the heart of making this possible is our AI-powered core computational geometry engine, purpose built for highly distributed cloud compute and manufacturing analysis. It is unlike anything else in the market, and designed with a deep blend of manufacturing and high-tech know-how from the very first line of code we wrote.
Right now, we specifically target precision machined components, but our long-term ambition is to become the focal point of how the world’s hardware innovators, tinkerers and makers secure the manufacturability of their design ideas.
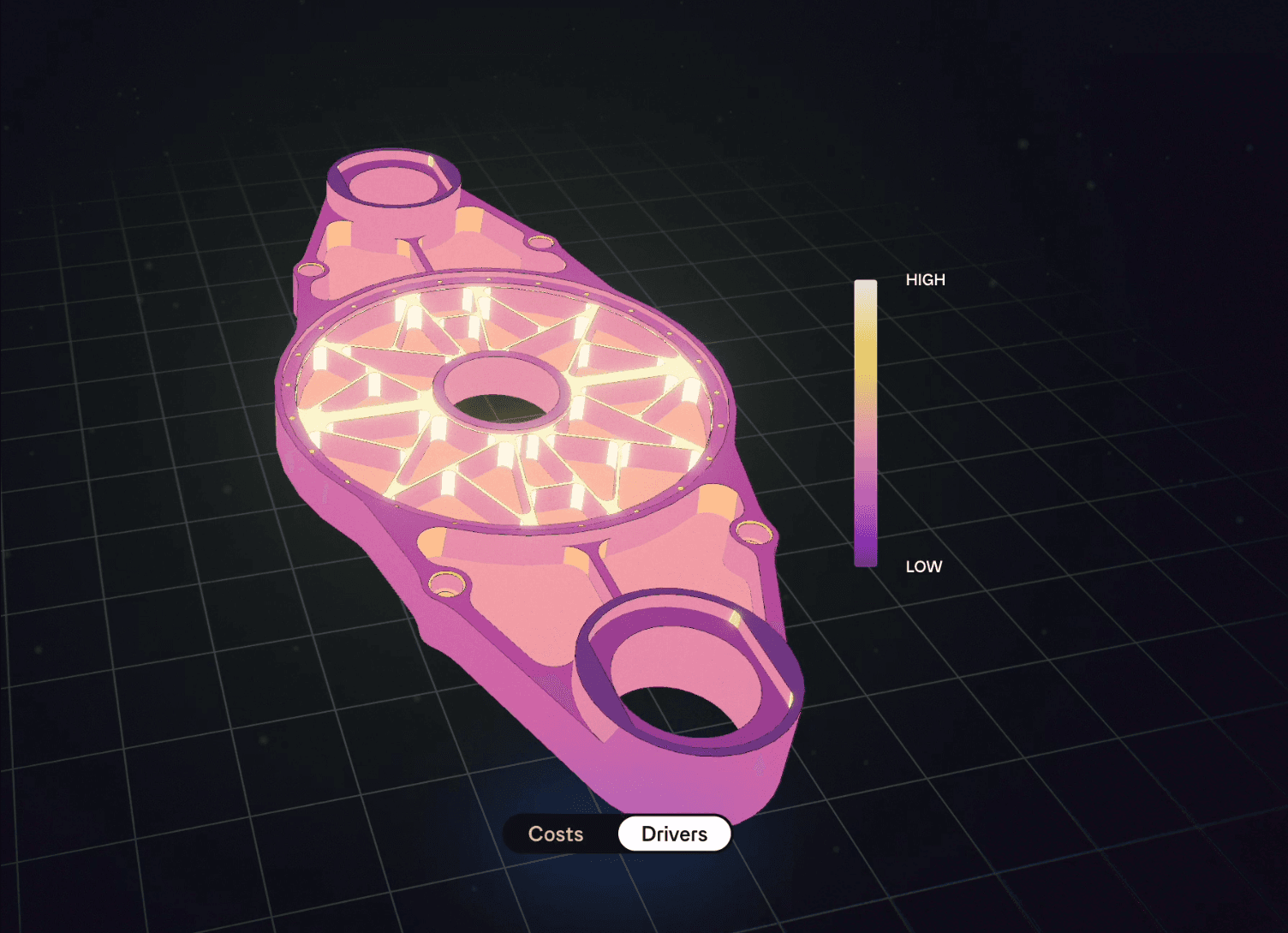
In the near term, we’ll start to share benchmarks of just how performant our engine is compared to the existing technology stack, both in terms of speed and scale of compute, as well as the level of automation it is capable of.
If you’re curious to learn more about what we’re up to, or interested in becoming an Encuber, don’t hesitate to reach out! We’re always interested in discussing the future of manufacturing, and working collectively to realize it.
Until then, upwards and onwards. Hugo Nordell, Co-founder and CEO
Machine things. Better
This is just a sneak peak of what we're up to. Reach out to learn more about how we're reimagining product industrialization at its core
About
We're encube, a deep tech software startup operating out of Sweden. We're fundamentally reimagining computer-aided industrialization for modern teams. It's collaborative, cloud-native, and highly AI-powered by design. Reach out to learn more and setup a demo session.
Resources
Check out our engineering blog to keep tabs on some of the more radical ideas we're pursuing.
Career
We have a trail. Now we need blazers. If you're head over heels for AI, distributed computing, computer graphics and want to work on truly impactful problems, drop us a note and we'll chat.
Get in touch
Interested in getting in touch with us? Drop us a note at contact@getencube.com, and we'll get the conversation started!